13. March 2025
, News
Clean air with clean connections
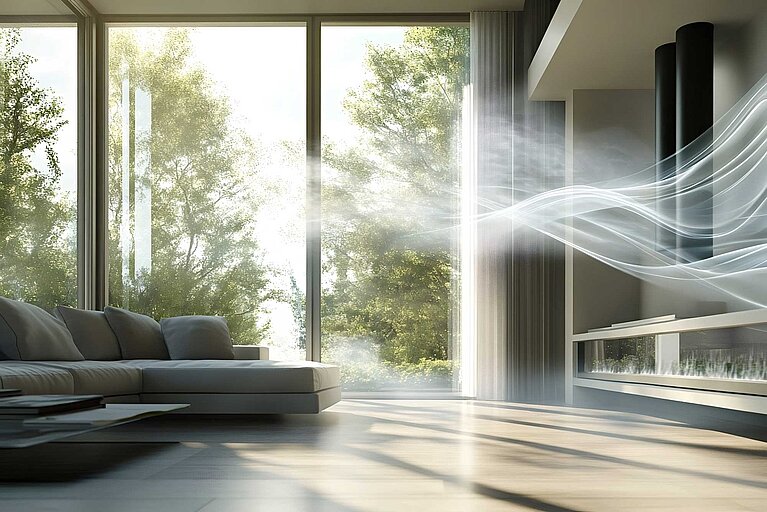
Ultrasonic welding has established itself as an efficient and precise joining technology in the manufacturing of plastic heat exchangers. It enables the tight, stable and material-friendly connection of components without the use of additional joining agents such as adhesives or screws. This process plays a particularly important role in applications involving aggressive mediums or high demands on tightness.
Commonly used adhesives release volatile chemicals (VOCs) during application or curing, a process known as outgassing. Adhesives containing solvents in particular release harmful substances such as acetone or toluene, which can irritate the respiratory tract. Water-based adhesives are less of a concern, but even these may outgas small amounts of volatile chemicals.
In ultrasonic welding, high-frequency mechanical vibrations (typically in the range of 20 kHz) are transmitted to the joining zone of the plastic parts. These vibrations create local heating through internal friction, which plastifies the contact surfaces and permanently connects them under light pressure. This creates a high-strength, homogeneous weld seam in short times from 200 to 300 milliseconds – depending on the application.
Not all plastics are equally suitable for ultrasonic welding. The following can be welded particularly well:
Ultrasonic welding is an essential joining technique for plastic heat exchangers. It enables tight, safe, and durable connections that meet the high demands of industry. The process offers significant advantages over conventional adhesive or screw techniques due to the combination of high process speed, low energy consumption, and excellent welding quality.
Learn more about the benefits of ultrasonic welding for your application and contact our team:
Heatexchanger@herrmannultraschall.com
Learn more about our ultrasonic welding technology in our free white paper: