17. March 2025
, News
How ultrasonics optimizes the manufacturing of hygiene products
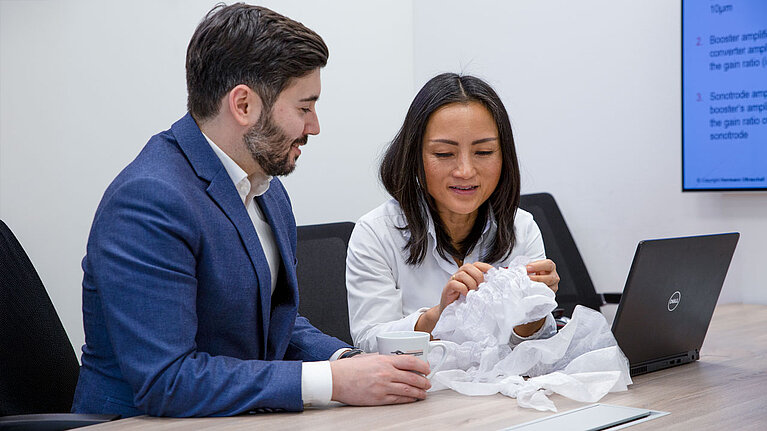
Diapers are an indispensable companion for babies or adults with incontinence problems. In addition to key aspects such as absorbency and leak protection, wear comfort is becoming increasingly important when selecting the right diaper. Consumers are paying more and more attention to products that feel soft on the skin and are comfortable to wear.
The softness of nonwoven materials plays a central role here. But how can the softness of the nonwoven material be preserved during the manufacturing of diapers and other hygiene products? Choosing the right bonding process is a key factor.
Unlike traditional processes, ultrasonic bonding does not require additional joining agents such as chemical adhesives. Instead, it uses high-frequency sound waves to join materials.
Vibrations are created and transmitted to the materials. This causes friction between the nonwoven layers at pre-determined locations, which generates heat for a short period of time. This heat causes the thermoplastic fibers in the nonwoven to melt. The result is a strong, cohesive bond without affecting the structure or properties of the material.
This efficient joining process allows very precise joints to be made without affecting the surrounding areas.
Soft nonwoven materials and comfortable diapers are a key selling point for consumers. With ultrasonic bonding technology, manufacturers can ensure that these requirements are met without compromising on functionality or costs.
The process ensures that the softness of the nonwoven materials – a crucial factor for wear comfort – is maintained. At the same time, companies can permanently save operational costs and energy by eliminating the use of joining materials such as adhesives.
Learn more about the advantages of ultrasonic welding for diapers, femcare and other hygiene products in our free white paper: