03. June 2025
, News
The benefits of ultrasonic welding for membranes used in filtration and venting
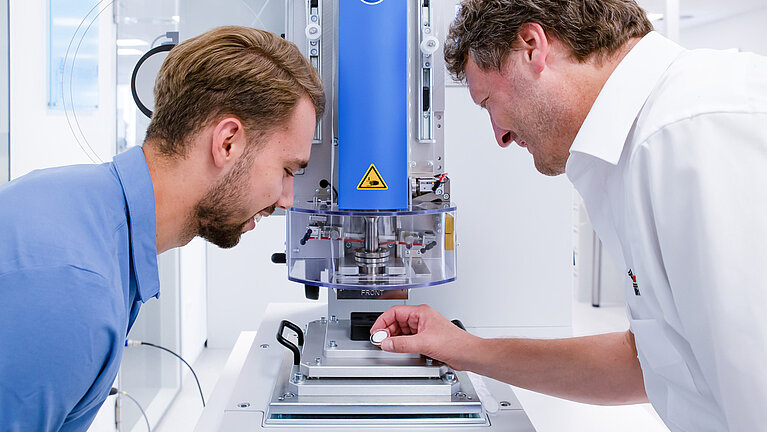
Whether in the automotive or medical industry, ultrasonic welding has established itself as a proven process for integrating membranes into applications with pressure equalization or filtration functions. Shorter process times and clean, reproducible results make this joining technology particularly attractive for automated production systems where the focus is on increasing output and efficiency.
When embedding membranes in a pre-syringe filter, for example, high-frequency mechanical vibration energy is introduced into the joining zone via a welding tool known as a sonotrode.
The resulting melt penetrates into the superficial pores of the membrane and forms a micromechanical anchoring there. This creates a tight, firm bond without additional additives such as adhesives.
Tip: You can find out which plastics are best suited to the ultrasonic welding process here:
Discover suitable plastics for ultrasonic welding
To shorten process times and further increase efficiency, our innovative ultrasonic joining process makes it possible to combine several work steps in a single automated process. The membrane is punched directly from a tape material and precisely embedded in the plastic component in a second step. This significantly reduces both material consumption and cycle times.
The process is carried out in four coordinated steps:
KACO was looking for a precise and fast joining process for embedding a membrane in an emergency degassing system.
The challenge: Despite its low weight and slight curvature, the membrane had to be positioned exactly in the centre of the housing. Inaccurate positioning could have impaired the functionality of the overall system.
Alternative joining methods, such as adhesive bonding, could not fulfil these criteria. In addition, the chemicals contained in the adhesive would have restricted the breathing activities of the fine membrane. The process cycles would also have been longer due to the drying time of the adhesive.
The solution: ultrasonic welding - precise and gentle on the material. Ultrasonic welding enables a permanent connection without the use of adhesives or other joining agents. This fully preserves the sensitive material properties of the membrane. Thanks to a customised tool solution and expert, application-specific process advice, the membrane can be positioned precisely in the component - reproducibly, reliably and with process safety.
Find out more about the customer benefits for KACO
In medical engineering, there is a growing demand for reliable joining processes with high automation potential. Ultrasonic welding of membranes offers decisive advantages over adhesive bonding or thermal sealing:
Gentle energy input: Even more sensitive filter media are joined reliably and without damage
Find out more about the benefits of ultrasonic welding in the medical industry here:
Ultrasonic welding for medical devices
Ultrasonic welding is an optimal solution for the reliable, clean and economical joining of membranes in plastic components. The process fulfils the highest requirements for tightness, process safety and reproducibility for membranes from leading suppliers such as Gore, Porex, Berghof and Schreiner.
Thanks to the gentle working method and precise controller of the welding parameters, even more sensitive membrane materials can be reliably and permanently connected. Easy integration into automated production lines and the possibility of seamless process monitoring make ultrasonic the preferred joining process for large-scale applications.
Sound consulting by ultrasonic experts is crucial here. They provide support with component design, process development and the integration of ultrasonic systems into existing or new production systems — enabling a smooth and fast start-up.